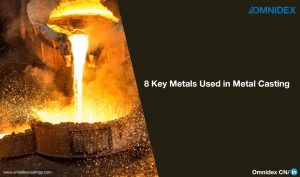
Our Locations
One-stop International Manufacturing Services
China Office
- 705, Building No.7, Beijiaochang Henglu 1, Guangzhou 510050, P.R. China
- +86 20 8388 7080
- info@omnidexgroup.com
Vietnam
- 3rd Floor, Sumikura Tower, 18H Cong Hoa Street, Ward 4, Tan Binh District, HCMC, Vietnam
- +86 20 8388 7080
- info@omnidexgroup.com
United Kingdom
- Unit 5, Lyneburn Industrial Estate, Dunfermline, Scotland KY11 4JT
- +44 (0) 1383 277077
- laser@omnidexgroup.com
For Other Locations
- Asia Pacific, South America, Africa and rest of the world:
- +86 20 8388 7080