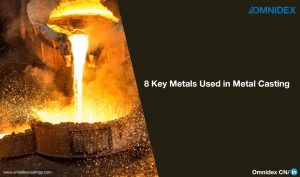
Case Study:
From Defective To Flawless Sand Cast Brackets
The problem part in question was a bracket whose primary function is to fix the air conditioning unit in vehicles. Made of ductile iron, sand casting is used to form these brackets with further machining and painting also employed to finish the product.