1. Cold-Chamber Conventional Die Casting
Cold chamber die casting machines are constructed such that the casting set is located separately from the melt reservoir. To produce a component, the alloy is filled into the casting chamber and pressed into the casting mold through channels.
This process is suitable for materials with a higher melting point. For example, aluminum die casting, but also copper.
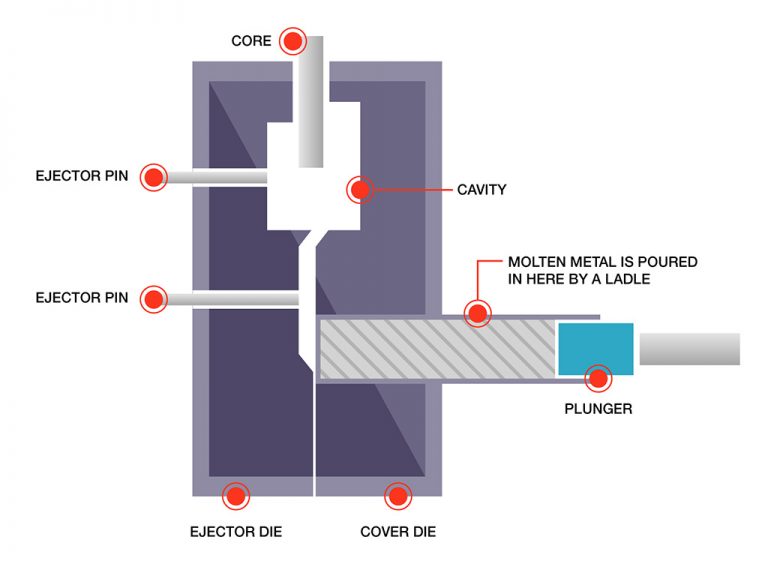