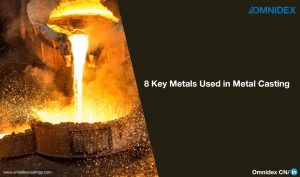
We are always ready to help with your latest project.
Contact our Customer Service and let us know how we can help to catapult your next project to success.
Cooling casting is a very complicated process. The most important part is the rate at which a casting cools down. Many properties of the casting are affected by this rate, which eventually determines the quality of the finished products.
In die casting processes, the quality of aluminium parts is greatly influenced by the temperature control of the mold. Nevertheless, cooling also has a decisive impact on the efficiency and speed of casting. You will learn how to minimize scrap rates and maximize product quality by optimizing and customizing cooling line control in this blog.
Cooling rate may seem like a trivial factor in the die casting process, but in reality, it has considerable effects upon the:
The cooling or control of the temperature influences the structure of the material, i.e. the microstructure and the surface of the metal. Errors, failures, or inaccuracies that occur during cooling have a direct effect on the quality of the cast product. Temperature control imperfections are not uncommon:
For example, flow fluctuations can occur – especially in systems with more than one cooling section running at the same time or with multiple die casting machines that are continuously supplied by the same central control system. It is essential that the cooling system calculates differences and compensates accordingly. Because heat must be dispersed uniformly across the final product, dissipation must be uniform at all points.
The cooling section must not only be fast in reaction but also be aligned and adjusted accurately to ensure the exact amount of cooling is applied where it is required: less cooling is needed at narrower areas of the product, while more cooling is needed at the wider zones to reduce internal thermal stress.
Another example, if a composite molded piece has uneven thickness on some areas, uneven cooling may occur, leading to undesirable microstructures and mechanical properties, these cause defects and weak spots to be scattered across the casting substrate.
Furthermore, the solidification cooling rate has far-reaching effects on the production and development cost of the product. Unexpected changes in microstructure and mechanical properties means additional processing (such as heat treatment or straightening processes) is needed on the product to meet the specifications.
As well as cost, additional processes may lead to more issues, such as the need to replace a non-heat-treatable alloy, excessive heat treatment causing surface blistering, and mechanical treatment inducing excessive residual stresses in the metal parts.
A professional die casting manufacturer will consider all these factors early in the development process. As an example Al-Si-Cu-Mg-Ni is an alloy that is very popular in the automotive industry, and is used to make die casted pistons and many other parts. let’s use this to explore the effect of cooling rates upon the mechanical properties and microstructure of die casting parts.
At lower cooling rates, the phase formed during the solidification is mainly M-Mg2Si phase, γ-Al7Cu4Ni phase, δ-Al3CuNi phase, ε-Al3Ni phase, and Q-Al5Cu2Mg8Si6 phase. When the solidification cooling rates are increased from 0.15 to 15°C/s, hardness increases from 80 to 125 HB, and tensile strength increases from 190 to 280 MPa.
If we increase the cooling rate still further, the alloy will solidify into a uniform structure and micro-hardness will increase from 130 to 196 HV.
For a complex cast product, more cooling channels will be required for cooling the mold. The sequence of the individual cooling channels is determined by the cooling strategy. Depending on the cooling channel, coolant time and quantity can be set separately. Liquid aluminum can be controlled very precisely regarding the direction of solidification. In this way, holes or cracks caused by uncontrolled shrinkage are reduced.
The solidification cooling rate has a great impact on the die casting process, as it may affect the alloy’s mechanical properties and dimensions, and subsequently the product quality.
The ability of a die casting system to regulate its internal temperature is vital to its success.
In order to avoid defects, different metals require different temperatures at which they will be properly forged, and a deviation outside these given temperature ranges will affect the final product. Furthermore, excessive temperatures can damage the less resistant components within a die casting system, resulting in equipment failures and costly maintenance downtimes.
Having a die-cast cooling system in place is the best defense against poor temperature regulation caused by casting. As a result, these devices will optimize process efficiency, protect critical equipment, and ensure high-quality parts.
Here at Omnidex, our casting engineers work tirelessly on casting simulation to optimize the cooling rates for every die casting product. Drawing upon our experience and expertise in metal casting, we will continue to deliver quality products to our valued customers. Get in touch with our casting engineers today to learn more about our cutting-edge die casting process.
mechanical properties
Omnidex is a World-Class Manufacturing and Engineering company that produces high quality, porosity-free casting products which are trusted by companies across different industries. Throughout the whole process, from product development to delivery, we strive to provide you with unwavering support. Providing you with unmatched diverse capabilities and experience, we help you overcome any obstacle.
Contact our Customer Service and let us know how we can help to catapult your next project to success.
If you are looking for metal casting services, our brochure is a great way to discover what Omnidex has to offer. You can download HERE or EXPLORE HERE to learn more.
Copyright © 2022 Omnidex Group. All rights reserved.
If you are looking for metal casting services, our brochure is a great way to discover what Omnidex has to offer. You can download HERE or EXPLORE HERE to learn more.
Copyright © 2024 Omnidex Group. All rights reserved.
This website uses cookies so that we can provide you with the best user experience possible. Cookie information is stored in your browser and performs functions such as recognising you when you return to our website and helping our team to understand which sections of the website you find most interesting and useful.
Strictly Necessary Cookie should be enabled at all times so that we can save your preferences for cookie settings.
If you disable this cookie, we will not be able to save your preferences. This means that every time you visit this website you will need to enable or disable cookies again.