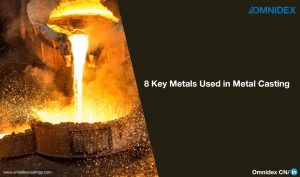
We are always ready to help with your latest project.
Contact our Customer Service and let us know how we can help to catapult your next project to success.
The process of sand casting involves the use of non-reusable sand molds to form metal castings. Casting appears to be a simple manufacturing process on the surface: anyone who has built a castle on the shore knows that sand can be used to form a variety of shapes. In a foundry, molten metal is held at high temperatures; successful operation depends on many factors.
Casting is used to make metal components ranging from several ounces to several tons. Molds made from sand can produce castings with fine exterior details, interior cores, and other shapes while it is possible to sand cast practically any metal alloy.
Silica sand, binder, moisture content, and additives are the main components of molding sand. The composition of a sand mold has a strong impact on the mold properties as well as the final casted product. Without an optimal sand mold composition, there is a risk for potential defects in the product.
Among the basic sand mold properties, they are porosity, flowability, collapsibility, adhesiveness, strength and refractoriness.
Shrinkage, sand drop, blowholes, pinholes, and scabs are the most common metal casting defects that can occur due to an inappropriate sand mold composition. Hardness, tensile strength, elastic modulus, and other mechanical properties can also affect if the quality of the sand molding is not suitable.
In a later article, we will discuss this topic in greater depth. Check back for updates!
It is therefore critical to have an optimized composition of the ingredients in sand molding. The fineness of the grain, the ratio of clay to water, binder additives (molasses, fly ash, dextrin, and scratch), and the degree of ramming, are key variables that must be considered before developing the sand molds.
But when the temperature gets over 800°C clay loses its plasticity and becomes a kind of dead clay. Molasses can act as an adhesive, helping to restore some of the plasticity lost in the dead clay. It can also help to enhance the compressive strength of the molds.
Nowadays, modern foundries prefer coal-free sand molds because of their reduced impact on the environment. But this can also have some undesirable effects on the sand mold properties and cause cracks and scabbing at high temperatures. Clay is also an important ingredient in a sand mold; it increases the bonding strength of the sand mold.
Research has also established that if fly ash is not present in a sand mold, then it loses its compatibility, tensile strength, and permeability. It is therefore essential to have a proper composition of these ingredients in the sand mold in order to have a defect-free product with better mold properties.
Our state-of-the-art production facilities allow Omnidex to provide high sand casting quality products without any metal casting defects. Our research and development team is constantly working to keep up to date with new research in the metal casting field. With years of effort and expertise, we have developed an optimized sand mold composition that provides us with the best quality output.
From the engineering point of view, we optimized sand mold compositions according to the type of material and operating temperature. Before starting the production, our engineers used statistical software to find the optimum composition of the sand molds based on their material types and operating temperature.
But we do not only rely on statistical models; our team has developed a large database of experimental data. So, whenever a new part has to be made, we predict the optimized sand mold composition through cutting-edge techniques such as machine-learning models.
mechanical properties
Omnidex is a World-Class Manufacturing and Engineering company that produces high quality, porosity-free casting products which are trusted by companies across different industries. Throughout the whole process, from product development to delivery, we strive to provide you with unwavering support. Providing you with unmatched diverse capabilities and experience, we help you overcome any obstacle.
Contact our Customer Service and let us know how we can help to catapult your next project to success.
If you are looking for metal casting services, our brochure is a great way to discover what Omnidex has to offer. You can download HERE or EXPLORE HERE to learn more.
Copyright © 2022 Omnidex Group. All rights reserved.
This website uses cookies so that we can provide you with the best user experience possible. Cookie information is stored in your browser and performs functions such as recognising you when you return to our website and helping our team to understand which sections of the website you find most interesting and useful.
Strictly Necessary Cookie should be enabled at all times so that we can save your preferences for cookie settings.
If you disable this cookie, we will not be able to save your preferences. This means that every time you visit this website you will need to enable or disable cookies again.