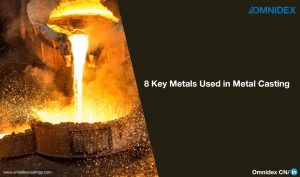
We are always ready to help with your latest project.
Contact our Customer Service and let us know how we can help to catapult your next project to success.
metal casting processes
This type of gating system is ideal for flat casting, which is achieved by filling the mold cavity with gravity. Generally, it is used in ferrous metal sand casting and in non-ferrous metal die casting processes.
This type of system is suitable for tall casting. It is used for high-pressure sand casting, shell mold casting, and die casting.
It is used in processes where molten metal is poured into the top space of a casting. This promotes directional solidification. During the filling process, the system is suitable only for flat casting to limit the metal’s damage.
It is used for tall castings. The metal enters slowly from the bottom of the cavity.
It basically combines the features of the bottom and top gates.
In designing a system, the position of the ingate(s) is extremely important. Additionally, it is important to use enough ingates such that the distance between the ingate, and any point that is filled by it, is smaller than the distance of molten metal fluidity. From the basin, the sprue usually flows both to the runners and to the ingates. The following 4 factors determine where the sprues are located.
The location should not be near hotspots.
It must be positioned in such a way as to reduce the size of the box surrounding the whole casting.
By allowing the molten metal to flow to other channels with minimal cooling, it reduces the chance of the gates breaking during fettling.
It is extremely important to get the mold filled in time, as this determines the final product’s quality. Slow fills can cause mis-runs and cold shuts, while quick fills can lead to solid and gaseous inclusions. It is possible to calculate the optical mold filling time in order to conduct an optimised operation.
Last but not least, the filling time is affected by factors such as the final function of the product, the pouring temperature used by die casters, the weight and minimum thickness of castings, as well as the velocity of the molten metal.
Omnidex is a leading manufacturer of aluminum and cast iron castings. We focus on manufacturing high-quality products. You can contact us by email if you have any questions or if you need metal casting foundry cooperation
Omnidex is a World-Class Manufacturing and Engineering company that produces high quality, porosity-free casting products which are trusted by companies across different industries. Throughout the whole process, from product development to delivery, we strive to provide you with unwavering support. Providing you with unmatched diverse capabilities and experience, we help you overcome any obstacle.
Contact our Customer Service and let us know how we can help to catapult your next project to success.
If you are looking for metal casting services, our brochure is a great way to discover what Omnidex has to offer. You can download HERE or EXPLORE HERE to learn more.
Copyright © 2022 Omnidex Group. All rights reserved.
This website uses cookies so that we can provide you with the best user experience possible. Cookie information is stored in your browser and performs functions such as recognising you when you return to our website and helping our team to understand which sections of the website you find most interesting and useful.
Strictly Necessary Cookie should be enabled at all times so that we can save your preferences for cookie settings.
If you disable this cookie, we will not be able to save your preferences. This means that every time you visit this website you will need to enable or disable cookies again.